現場の改善は進めている。センサーやPLCもすでに導入済み。
——それでも、「効率化が実感できない」「データはあるのに活かせていない」そんな声をよく耳にします。
工場のIoT化が注目されて久しい今、重要なのは単なる設備投資ではなく、“全体を見て活かす”仕組みづくり=データの統合と可視化です。
そこでカギとなるのが、SCADAと呼ばれる産業用IoT基盤。各機器からの情報をリアルタイムで取得・集約し、“つながる現場”をつくる中核的な役割を果たします。
この記事では、工場の効率化とIoT化を進める上でSCADAが果たす役割とその導入メリットについて、国内で最先端のSCADAソリューション「N3uron」を提供するSCADAWORXの支援事例やノウハウを交えてご紹介します。
「どこからIoTを始めればよいかわからない」「現場に負担をかけずに可視化したい」という製造業の皆さまに、最適な一歩をお届けします。
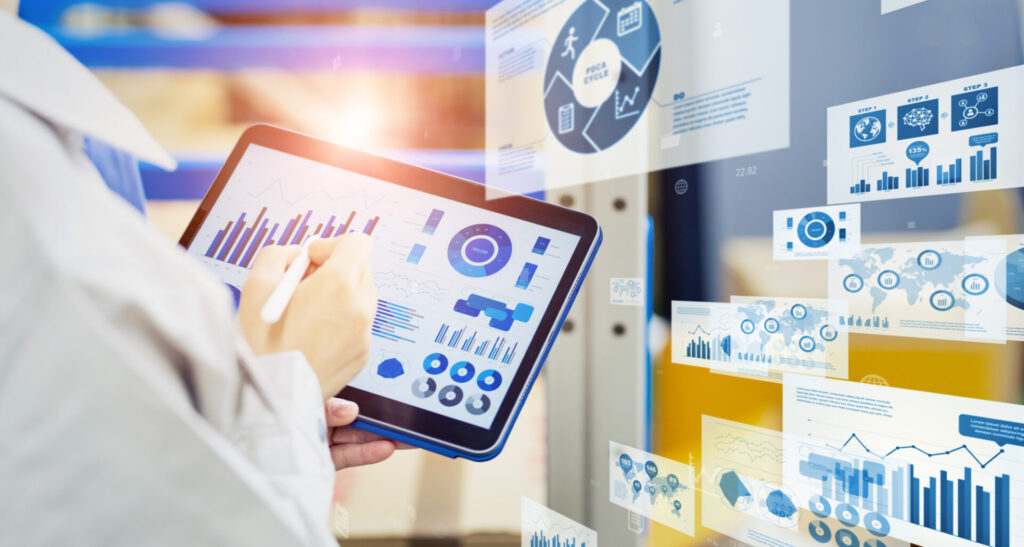
なぜ今、工場の「IoT化と効率化」が不可欠なのか
需要変動に柔軟に対応する工場が求められている
消費者ニーズの多様化や地政学的リスクの高まりにより、製造現場にはこれまで以上に「柔軟な対応力」が求められる時代になりました。
たとえば、同一設備で異なる製品を切り替えて生産する「多品種少量生産」や、グローバルな需給バランスを見ながらの生産調整などが当たり前のように行われています。
こうした変化に対応するには、現場の状況をリアルタイムで把握し、状況に応じて即座に判断できる情報基盤が必要です。
単なる人海戦術や過去の勘に頼った対応では、複雑化・高速化するモノづくりの現場についていくことが難しくなっています。
人手不足時代における“省力化”から“自律化”への転換
少子高齢化の影響により、製造業も深刻な人手不足に直面しています。特に地方の中小工場では、24時間体制を維持するための人材確保すら困難という声も少なくありません。
このような背景から、現場では「省力化」だけでなく、設備やシステムが自律的に判断し、必要なアクションをとる“自律化”の必要性が高まっています。
IoT化はその第一歩。センサーやネットワークを通じて工場の動きを「見える化」し、人がいなくても判断できる環境を整えることが、これからの製造現場には不可欠です。
「設備があるだけ」では進まないデジタル化の落とし穴
「うちの工場はIoT対応済みです」という企業でも、実際には機器ごとのデータがバラバラに管理されているケースがよくあります。
センサー、PLC、制御盤、検査装置……それぞれの情報が独立して存在し、全体のつながりが可視化されていないのです。
このような状態では、いくら高性能な設備を導入しても、現場の判断や改善につなげることはできません。重要なのは、データを一元的に集約・分析・可視化し、“工場全体でつながった情報”として活用することです。
その中核を担うのが、SCADAというIoT化の基盤システムなのです。
工場のIoT化に立ちはだかる3つの導入障壁
システムが複雑で社内に知見がない
IoT化の必要性は理解していても、「どこから手をつければよいのか分からない」と感じている工場管理者は少なくありません。
複雑な通信プロトコルや、PLC・センサー間の連携、クラウドとオンプレミスの使い分けなど、専門的な知識が要求される場面が多く、現場にはノウハウが不足しているのが実情です。
このような状況では、「やりたいけど進められない」「ベンダーに任せきりで現場が活用できていない」といった“失敗するIoT導入”が起こりがちです。
運用のハードルを下げ、現場でも使いこなせる仕組みが必要です。
既存設備との互換性や連携に不安がある
既に工場には多くの生産設備や測定装置が導入されており、それらはメーカーや世代が異なるため、統一した監視・制御が難しいと感じる企業も多いでしょう。
「新しいIoTシステムが、今ある設備とうまくつながるのか?」という疑問は、導入をためらう大きな要因のひとつです。
また、設備ごとに異なるソフトウェアや通信方式が存在していると、データの統合管理が困難になり、むしろ運用負荷が増してしまう可能性すらあります。
この課題に対応できるのが、多様な通信プロトコルに対応し、機器を“つなぐ”機能を持つSCADAです。
費用対効果が見えづらく、投資判断が難しい
IoTやDXは中長期的な投資として語られることが多く、すぐに目に見える効果が出にくいことも、導入をためらう理由のひとつです。
特に経営層に対して、「このシステムを導入することで何が変わるのか」「どのくらいの期間で回収できるのか」を明確に示す必要があります。
SCADAを導入することで得られる、停止時間の短縮・保守業務の自動化・品質の安定化・省人化の実現といった効果を定量的に可視化できれば、IoT投資に対する社内の理解と納得も進みます。
SCADAが工場のIoT化を推進する理由とは?
現場データをリアルタイムに“つなぎ・見せる”統合力
SCADA(Supervisory Control and Data Acquisition)は、もともと工場設備を監視・制御するためのシステムとして使われてきましたが、近年ではその枠を超え、IoT化の中核インフラとして注目されています。
その最大の理由は、多様な機器・センサー・システムを“ひとつにつなぐ”統合力にあります。
たとえば、PLCや制御装置、検査装置、エネルギー管理システムなど、異なる通信プロトコルを使う機器を同一プラットフォーム上で統合管理できるのが、SCADAの大きな強みです。
「つながらない機器がない」というほどの柔軟性を持つSCADAは、IoT化の土台として極めて有効です。
導入後すぐに実感できる業務効率とダウンタイムの削減
IoT導入では「すぐに効果が出ないのでは」という不安もありますが、SCADAはリアルタイムのデータ収集とアラート通知ができるため、導入初期から業務効率化やトラブル対応の迅速化といった成果を実感できます。
たとえば、これまで目視確認に頼っていた設備の異常監視が、アラート通知によって瞬時に把握可能になり、対応までの時間を大幅に短縮。
また、設備の稼働率や停止理由をデータで記録・分析できるようになることで、定期点検の最適化や無駄な停止の削減にも直結します。
OTとITの橋渡しで、部門間の“サイロ化”を解消
製造現場(OT)と情報システム部門(IT)の間には、目的や言語の違いから連携が難しいという課題が常に存在しています。
この「部門間の壁」が、IoT導入やDX推進の障害となるケースは非常に多いのが現実です。
SCADAはその橋渡し役として、OTから得られたリアルタイムデータを、ITシステムで活用できる形式に変換・統合する役割を果たします。
たとえば、ERPやBIツールとの連携を通じて、製造データを経営判断に活かせる形で提供することも可能です。
つまり、SCADAは現場と経営、設備とIT、個別装置と全体最適をつなぐ、“IoT時代のハブ”ともいえる存在なのです。
SCADA導入によって得られる5つの実用的メリット
1. 設備状態の可視化による早期異常発見
SCADAを導入する最大のメリットのひとつは、リアルタイムでの設備状態の監視です。
温度、圧力、振動、電流などのセンサーデータを常時取得し、あらかじめ設定した閾値を超えると自動でアラートを発信。これにより、突発的なトラブルを未然に防ぐことが可能になります。
また、複数の設備データを並列で表示することで、全体のバランスや連動性の乱れにも気づきやすくなり、現場の判断スピードが格段に上がります。
2. 遠隔監視・遠隔制御による人員最適化
SCADAは、現場にいなくても工場内の状況を遠隔から把握・操作できる仕組みを提供します。
これは多拠点工場や夜間無人稼働、災害時の安全対策などにも効果的で、監視業務の省人化・省力化につながります。
たとえば、地方拠点の工場を本社からモニタリングしたり、トラブル時に現地担当者へ正確な指示を送るなど、人の移動や時間のロスを最小限に抑える運用が可能です。
3. 定型業務の自動化で管理負担を軽減
従来は手作業で行っていた日報作成や稼働率計算、点検チェックリストの作成なども、SCADAがあれば自動的にログデータをもとに帳票出力やレポート作成が可能です。
これにより、現場管理者や保全担当者のルーチン業務を大幅に削減し、本来注力すべき改善活動や品質分析に時間を充てることができるようになります。
結果的に、現場の「考える力」が最大限に活かされる体制へとつながります。
4. 過去データ活用による品質・歩留まり改善
SCADAはリアルタイム監視だけでなく、過去の運転データを時系列で蓄積・分析する機能を備えています。
これにより、品質トラブルが発生した際の「過去追跡」や、歩留まりの変化に関する「傾向分析」が容易になります。
たとえば、「良品が多く出るときの機械条件」と「不良品が出やすい条件」を比較することで、最適な運転設定や品質基準を導き出すことも可能です。
5. 他システムとの連携による全体最適の実現
SCADAは、ERPやMES、BIツールなど他のITシステムと柔軟に連携できます。これにより、現場で取得したデータを経営判断や生産計画、在庫管理、購買予測などに直結させることができ、
単なる現場管理ツールではなく「全社最適化を推進する基盤」として機能します。
IoT化の真の目的は、現場を変えることだけではありません。企業全体の価値創出サイクルを改善することにあります。SCADAは、その橋渡しを担う存在なのです。
IoT化の成功には“導入後”の運用設計がカギ
「使われないデータ」にしないための現場巻き込み
IoT化やSCADAシステムの導入後、ありがちな課題のひとつが「データは取れているが、現場では活用されていない」という状態です。
これは、導入段階で現場とのすり合わせが不十分だった場合に起こりやすく、データ表示が「分かりにくい」「見たい情報が出てこない」などの不満につながってしまいます。
そこで重要なのは、導入初期から現場の担当者を巻き込み、「どう見せると判断しやすいか」を一緒に設計していくことです。
SCADAはカスタマイズ性が高いため、ユーザーごとに最適なUI設計や表示設定が可能です。現場が「これは使える」と実感できる仕組みにすることが、運用の定着と効果の最大化につながります。
SCADA導入を全社DXの起点にする方法
IoTやSCADAの導入は、単なる現場改善の手段にとどまりません。得られたデータを活用すれば、経営層が意思決定に使える指標の可視化や、営業・調達・在庫などの部門をまたいだ連携にもつながっていきます。
たとえば、「設備の稼働率×納期管理×在庫情報」がリアルタイムで連携されていれば、納期遅延リスクの予測や、需給バランスに基づく生産調整も可能になります。
このように、SCADAは“全社の情報インフラ”として活用できる伸びしろが大きいツールです。
SCADAWORXでは、こうした現場視点と経営視点を両立させた導入・運用支援も行っており、単なるシステム納品ではなく、「工場の仕組みそのものを変える」ための支援が特徴です。
段階的にスモールスタートできるスキームとは
「すべての工場を一気にIoT化するのは難しい」と考える企業も多いでしょう。
その場合でも、SCADAを使えばまずは1ライン・1設備からのスモールスタートが可能です。
たとえば、最初は「1つの設備の稼働監視+異常通知」から始め、効果が見えた段階でライン全体→複数工場へと段階的に展開することができます。
また、ライセンス制やクラウド連携に対応したSCADAであれば、初期コストを抑えながら柔軟な拡張が可能です。
SCADAWORXが提供する「N3uron」は、まさにこの段階導入・拡張性の高いSCADAとして、工場規模を問わず多くの企業に選ばれています。
まとめ|SCADAはIoT化における“投資価値の高い土台”
工場のIoT化や効率化を進めるうえで、最も重要なのは「つながる仕組み」と「使えるデータ」を整備することです。
高価な機器やセンサーを導入しても、それらの情報がバラバラで活かせなければ、投資効果は限定的になってしまいます。
SCADAは、工場の設備・センサー・人・システムをリアルタイムでつなぎ、ひとつの画面に集約する“情報のハブ”として、
IoT化の基盤を支える役割を果たします。単なる監視ツールではなく、「効率化の実行支援」「改善活動の起点」「DXの土台」として、極めて高い投資価値をもつソリューションです。
特に、SCADAWORXが提供するSCADAプラットフォーム「N3uron」は、拡張性・操作性・導入支援体制に優れた次世代SCADAとして、国内外の工場での導入実績が広がっています。
現場に寄り添った導入支援と、段階的なIoT化戦略が可能なSCADAWORXのサポートは、初めてのIoT導入でも安心して進められる体制です。
「どこからIoT化を始めればいいか分からない」
「現場に負担をかけずに効率化を実現したい」
「投資対効果が見える仕組みがほしい」
――そんなお悩みをお持ちの方は、ぜひ一度、SCADAWORXによるSCADA導入のご相談・資料請求をご検討ください。
IoT化に踏み出す第一歩は、“つながる現場”づくりから始まります。